Ein kurzer Tritt – klack – Gang rein und ab geht die Post. Aber wie kommt das Gangrad in Sekundenbruchteilen in seine Position? Und wie wird garantiert, dass in der Eile nicht zwei Gänge zugleich einrasten, was für Getriebe und Fahrer einem GAU gleichkommen würde. Zudem stellt sich die Frage, wie die variablen Gangräder die brutal einhämmernde Motorleistung in Verbindung mit schlampig eingekickten Schaltvorgängen überleben?
0,10 Sekunden für den reinen Schaltvorgang
Um zu verstehen, was in einem konventionellen Motorrad-Klauengetriebe abläuft, spulen wir den Schaltvorgang in Zeitlupe ab und beobachten, wie sich die Drehbewegung am Schalthebel zu einer axialen Verschiebung der Zahnräder entwickelt. Der erste Gang ist ausgedreht, das maximale Drehmoment sorgt für eine rasante Beschleunigung. Kurz vor dem roten Bereich, also der maximalen Motordrehzahl, nimmt der Fahrer das Gas weg, zieht die Kupplung und schiebt den zweiten Gang ein. Dabei bewegt er den Schalthebel rund 30 Millimeter nach oben – beziehungsweise bei Rennstrecken-Konfiguration nach unten. Hurtige Piloten benötigen dafür rund 0,15 Sekunden, bis die Kupplung wieder eingerückt, die Zugkraftunterbrechung beendet ist und die Drosselklappen auf Vollgas stehen.
Für den reinen Schaltvorgang vergehen hingegen nur rund 0,10 Sekunden, in denen der erste Gang aus seiner Position befördert wird und anschließend das zweite Gangrad rund sechs Millimeter axial auf der Getriebewelle verschoben wird, damit die Schaltklauen sicher einrasten.
Umwandlung der Drehbewegung am Schalthebel
Um die Umwandlung der Drehbewegung am Schalthebel in eine lineare Verschiebung zu bewerkstelligen, sind einige mechanische Schritte notwendig. Als Erstes muss die Drehbewegung der Schaltwelle auf die Schaltwalze übertragen werden. Dafür gibt es unterschiedliche Möglichkeiten in Form von Zähnen, einer Hebelübersetzung oder einer Klinken-Mechanik. Alle Systeme sind mit einer Ratschenmechanik ausgestattet, die es der Schaltwelle erlaubt, die Schaltwalze um bestimmte Winkelgrade zu verdrehen, um dann wieder in ihre ursprüngliche Position zurückzukehren. Erst die in die Schaltwalze eingefrästen Nuten formen die Rotation in eine lineare Bewegung um und transportieren die sogenannten Schieberäder durch die Kulisse auf der Schaltwalze in ihre Position.
Bedingt durch die blitzschnellen Abläufe des mechanischen Vorgangs entstehen Reibung und Massenkräfte. Beides kann man bei Sport- und Rennmaschinen allerdings überhaupt nicht gebrauchen, weil dort eine unnötig lange Zugkraftunterbrechung am Hinterrad Fahrwerksunruhen und Zeitverluste bewirkt. Bei qualitativ hochwertigen Sportmotoren drehen sich deshalb Schaltwelle und Schaltwalze in Nadel- oder Kugellagern, um die Reibung bestmöglich zu reduzieren. Bei professionell aufgebauten Rennmaschinen reduzieren zusätzlich nadelgelagerte Schalthebel und spielfreie, leichtgängige Qualitäts-Kugelköpfe oder gar nadelgelagerte Schaltgestänge Reibung und Spiel der Schaltkonstruktion auf ein Minimum.
Leichtbauteile gegen Massenträgheit
Der Massenträgheit im Getriebe rückt man mit Leichtbauteilen zu Leibe. So sind die Stahl-Schaltwalzen meist hohl gegossen und/oder weitgehendst abgefräst. Noch effizienter sind Schaltwalzen aus einer hochfesten Alu-Legierung. Diese erlauben eine blitzschnelle Rotationsbewegung der Walze, die dabei vom sogenannten Schaltstern unterstützt wird. Dieser hat die Aufgabe, durch das Nockenprofil und eine federbelastete Rolle die Schaltwalze absolut zuverlässig zu arretieren. Spitze Nockenformen sorgen zudem dafür, dass die Schaltwalze durch die Federkraft beim Einrücken des Gangrades beschleunigt und der Schaltvorgang somit verkürzt wird.
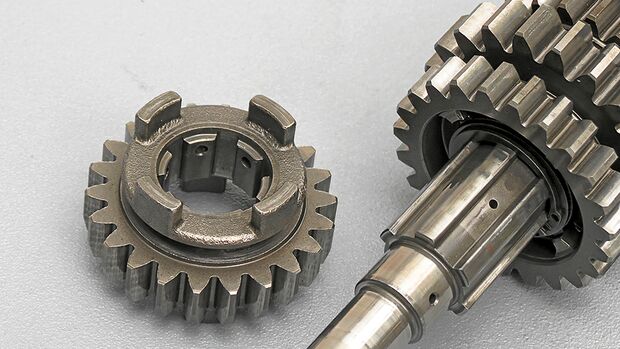
Das Getriebe selbst besteht aus der sogenannten Eingangswelle, auf deren Ende die Kupplung sitzt und die Kraft einleitet, und der Ausgangswelle, deren Ende aus dem Motorgehäuse herausragt und das Kettenritzel aufnimmt. Für jede Gangstufe steht ein Zahnradpaar zur Verfügung. Da diese ständig im Eingriff sind, müssen diese Paarungen aus je einem Fest- und einem Losrad bestehen. Losräder sind nicht fest mit der Welle verbunden, sondern drehen sich auf Nadel- oder Gleitlagerbuchsen frei auf der jeweiligen Getriebewelle. Die Festräder sind starre, nicht verschiebbare und auf die Welle gefräste oder aufgepresste Zahnräder. Der Kraftschluss zur Welle wird durch die Schieberäder hergestellt, die sich auf einer Verzahnung seitlich verschieben lassen und mit den Klauen in die Aussparungen der Losräder eingreifen.
Womit auch die Losräder eine formschlüssige Verbindung im Antriebsstrang erhalten. Das Problem der doppelten Schieberäder ist das hohe Gewicht, dass bei schnellen Schaltvorgängen enorme Massenkräfte freisetzt, weshalb die Schaltgabeln eine hohe Biegesteifigkeit aufweisen müssen.
Renngetriebe vs. Tourengetriebe
Die Übersetzungen der jeweiligen Gangstufen richtet sich nach dem Einsatzzweck und der Motorcharakteristik. Sport- und Renngetriebe werden so ausgelegt, dass man auf der Rennstrecke alle Gangstufen nutzen kann, um die Drehzahlsprünge beim Schalten so gering als möglich zu halten. Also wird der erste Gang relativ lang übersetzt, die restlichen Stufen sind zunehmender enger ausgelegt. Dies garantiert, dass man sich bei hoher Geschwindigkeit und entsprechend hohem Fahrwiderstand (Luftwiderstand plus Rollwiderstand) im günstigsten Drehmoment- und Leistungsbereich aufhalten kann. Tourenmaschinen hingegen werden immer öfter mit einem auffallend langen sechsten Gang ausgestattet, der die Drehzahl deutlich absenkt und somit material- und kraftstoffsparend wirkt.
Sanftester Lauf bei Getrieberädern mit Schrägverzahnung
Die Zahnformen der Getrieberäder sind entscheidend für den möglichst leisen Lauf des Getriebes. Wobei die Kombination aus Eingriffwinkel, Profilverschiebung, Modul und zig anderen Faktoren eher als Betriebsgeheimnis gehandelt wird. Den sanftesten Lauf weisen zweifellos Getrieberäder mit einer Schrägverzahnung auf. Solche Getriebe verlangen jedoch nach einer gänzlich anderen Art der Schaltung, wobei der Kraftfluss nicht über Schieberäder, sondern über sogenannte Schaltmuffen hergestellt wird. Der Vorteil von Schaltmuffen: Sie lassen sich aufgrund des geringen Gewichts extrem schnell und leicht verschieben, weshalb gerade im Rennsport mit solchen Getrieben laboriert wird. Der Nachteil: Die Getriebewellen bauen etwas länger als bei Klauengetrieben, bei denen die kompletten Zahnräder verschoben werden.
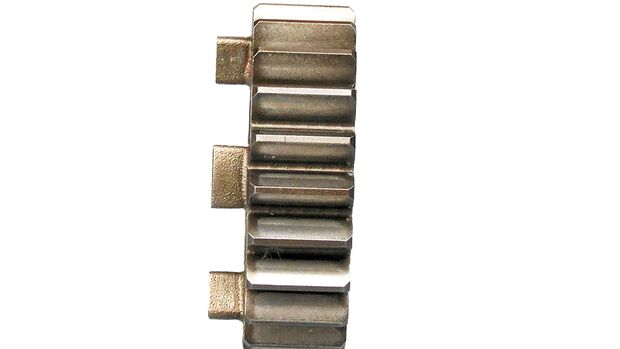
Die Schaltbarkeit eines Getriebes hängt von vielen Faktoren ab. Neben der bereits erwähnten mechanischen Reibung spielen die Schaltkurve auf der Schaltwalze und die Anordnung und freien Verdrehwinkel sowie die Anzahl der Klauen eine große Rolle. Schließlich müssen diese bei voller Getriebedrehzahl – also etwa einem Drittel der Motordrehzahl – ihre Position wechseln. Um zu garantieren, dass die Gangräder fest in ihrer Position verharren, sind bei leistungsstarken Maschinen die Klauen mit einem Hinterschliff von rund vier Grad versehen. Dieser Hinterschliff sorgt dafür, dass sich miteinander verbundene Getrieberäder unter Last regelrecht „anziehen“.
Ein widerstandsloser Schaltvorgang ist rein rechnerisch nur bei etwa jedem zweiten Gangwechsel möglich. Nämlich dann, wenn die Klauen exakt mit den Aussparungen am benachbarten Gangrad fluchten. Ist dies nicht der Fall, drückt die Schaltgabel das Getrieberad in die sogenannte „Klaue-auf-Klaue“-Position, wodurch sich der Schaltvorgang so lange verzögert, bis sich die Getrieberäder so weit verdreht haben, dass die Klauen ineinander schlüpfen können. Je größer der freie Verdrehwinkel, also das „Spiel“ von Klauenanschlag zu Klauenanschlag, desto größer die Chance eines sauberen Schaltvorgangs. Mit dem Nachteil, dass sich dieses Spiel auf das Lastwechselverhalten negativ auswirkt. Deshalb suchen die Konstrukteure meist den besten Kompromiss aus leichter Schaltbarkeit und einer direkten, ruckarmen Kraftübertragung.
Je größer die Gangspreizung, desto härter der Schaltvorgang
In der Regel gilt: je größer die Gangspreizung, desto härter der Schaltvorgang. Der Grund: Die große Drehzahldifferenz zwischen den einrastenden Zahnrädern verhindert einen einigermaßen synchronen Lauf, die Klauen rattern entsprechend hart in die Aussparungen. Ähnlich verhält es sich bei vielen Maschinen beim Einlegen des ersten Gangs, das oft mit einem lauten, harten Schaltschlag die Aufmerksamkeit der Passanten weckt. Meist ist eine durch das Motoröl verklebte Kupplung Hauptursache für dieses Malheur.
Auch Motorschwungmassen, das Schleppmoment zwischen Kurbelwelle und Hinterrad – Stichwort verklebte Kupplung – und die Ruckdämpfer im Antriebsstrang beeinflussen je nach Drehzahl den Schaltvorgang. Rasante Gangwechsel nach oben sind durchaus auch ohne Betätigung der Kupplung möglich, schließlich reicht ein kurzes Entlasten des Antriebsstrangs, um die Getrieberäder zu verschieben. Allerdings glückt ein solcher Schaltvorgang nicht immer, was dazu führt, dass die Klauen hart und mit lautem Schaltschlag einrasten. Nahezu perfekt hingegen regeln gute elektronische Schaltautomaten diesen Vorgang. Dabei genügt es jedoch nicht, einfach für ein paar Millisekunden die Zündung lahmzulegen. Nur wenn Motordrehzahl und Schaltposition berücksichtigt werden, kann eine clevere Elektronik, die zum Beispiel noch einen Zwischen-Zündfunken auslöst, den Schaltvorgang nicht nur auf etwa 2/100 Sekunden verkürzen, sondern auch das Getriebe schonen und das Fahrwerk beim Beschleunigen stabilisieren. Wie die Motorkraft über Kette und Kardan ans Hinterrad gereicht wird und sich das Drehmoment auf Schwinge, Federung und Kurvenverhalten auswirkt, steht in PS 12/2013.
Getriebe-Schäden
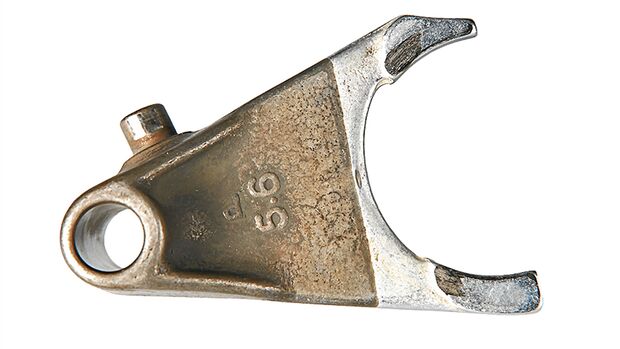
Sind die Schaltklauen an den Kanten verschlissen und regelrecht verrundet, dann drücken sich unter Last die Schieberäder gegen die Führung der Schaltgabel nach außen. Die Folge: Die Gänge können herausspringen, die Schaltgabeln reiben sich an den Führungsflächen auf oder verbiegen sich. Womit eine Kettenreaktion ausgelöst wird, die darin endet, dass die Getrieberäder mitsamt Schaltgabeln erneuert werden müssen.
Oberflächenausbrüche, sogenanntes Pitting, gehören zu den häufigsten Getriebeschäden. Ursache sind meist zu kleine Dimensionierung, falsches Härteverfahren oder ungünstige Zahnformen. Im Dauerbetrieb werden solche Zahnräder durch die hohe Flächenpressung zerstört.
Tipps und Tricks
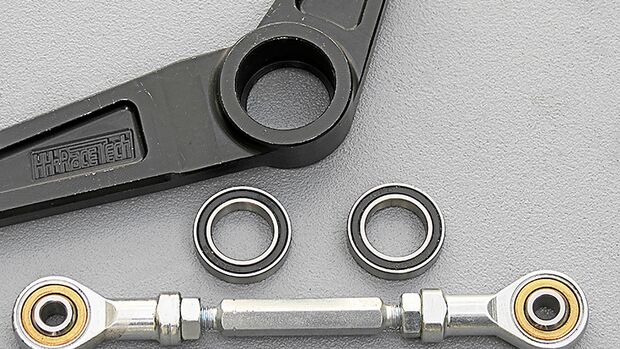
Um eine Serienschaltung zu optimieren, sollte zuerst kontrolliert werden, ob das Schaltgestänge im 90-Grad-Winkel zum Schalthebel steht. Nur so stimmt die Hebelwirkung der bei der Konstruktion festgelegten Kinematik.
Die oft billigen Kugelgelenkköpfe können durch hochwertige und leichtgängige Bauteile ersetzt werden (z.B. Askubal, Durbal, SKF). Dazu müssen unter Umständen die serien- mäßigen Bolzen aus den Schalthebeln ausgebohrt werden.
Schalthebel mit leichtlaufenden und spielfreien Kugellagern (HH-Racetech) verbessern Schaltgefühl und Leichtgängigkeit. Auch weit außerhalb der Fußrastenachse gelagerte Schalthebel stören den flüssigen Gangwechsel, da die Drehebenen zu weit auseinander liegen und sich der Stiefel für den Längenausgleich über den Schaltknauf schieben muss.